Engineering plastics are used in a wide range of industries and applications, from automotive parts to medical devices. They are an integral part of modern life, and as such, understanding what these materials are can be beneficial for anyone interested in design or engineering. Engineering plastic is also known by a number of different names, depending on its specific properties. This article will delve into the different names that engineering plastic might be referred to, as well as the characteristics that make it so useful.
What is Engineering Plastic?
Another name for engineering plastic is advanced or high-performance plastic. It refers to a group of polymers that are designed to meet specific performance requirements, such as improved strength, durability, and resistance to heat and chemicals. These materials have become increasingly popular in various industries due to their ability to replace traditional metal components that are heavier and more expensive.
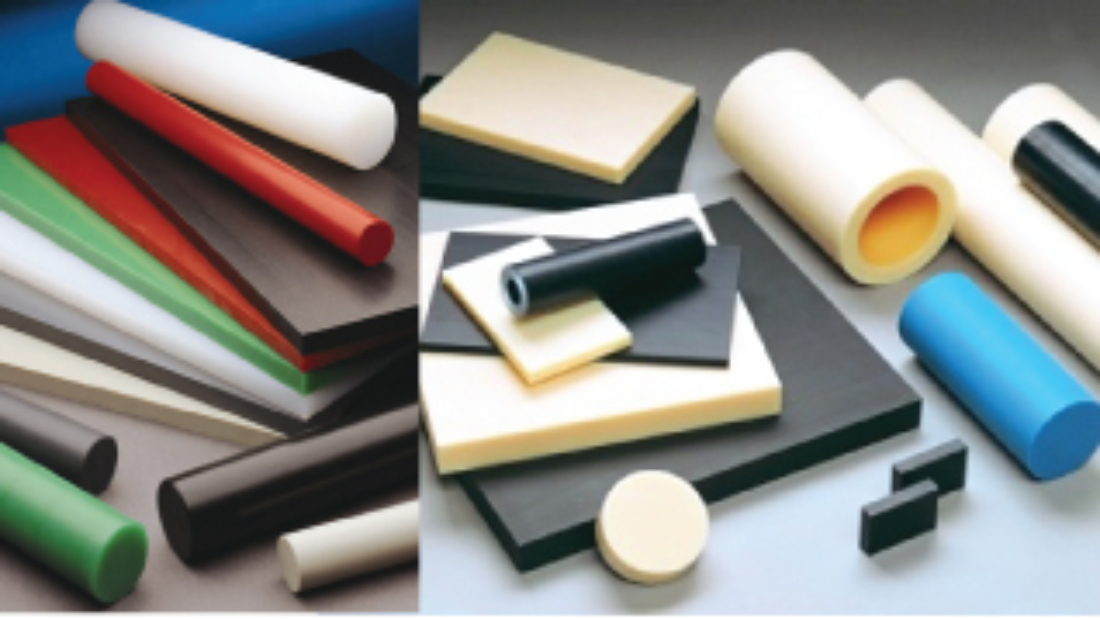
Engineering plastics offer several advantages over conventional plastics, including superior mechanical properties such as high tensile strength and impact resistance. They also have excellent dimensional stability in harsh environments with extreme temperature variations. This makes them ideal for applications where weight reduction is critical but strength cannot be compromised.
Overall, engineering plastics have become an essential part of modern day manufacturing processes due to their versatility and enhanced performance capabilities. From automotive parts to medical devices, these materials continue to revolutionize the way we design and manufacture products while improving overall efficiency and cost-effectiveness.
Types of Engineering Plastics
Engineering plastics, also known as advanced or technical plastics, are a group of materials that offer superior mechanical and thermal properties compared to traditional thermoplastics. There are many different types of engineering plastics available, each with their own unique set of characteristics.
One common type of engineering plastic is acetal, also known as polyoxymethylene (POM). Acetal has excellent dimensional stability and low friction properties, making it ideal for use in high-performance parts such as gears and bearings. Another popular engineering plastic is polycarbonate (PC), which has exceptional impact resistance and optical clarity, making it suitable for applications like safety glasses and electronic components.
Other types of engineering plastics include nylon (PA), which offers high strength and good chemical resistance; polyphenylene oxide (PPO), which has excellent electrical insulation properties; and polyetherimide (PEI), which combines high strength with temperature resistance. Overall, the versatility of engineering plastics makes them an essential material choice for a wide range of industrial applications.
Properties of Engineering Plastics
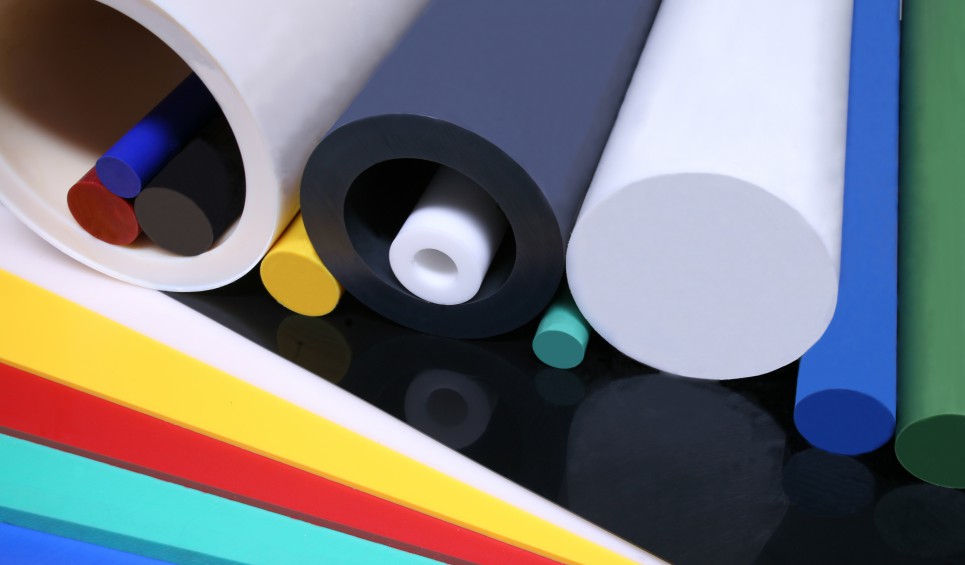
Engineering plastics, also known as advanced or high-performance plastics, are a group of materials specifically designed to withstand extreme conditions and environments. They exhibit unique properties such as high strength, stiffness, heat resistance, and low friction coefficient. These materials can replace metals in many applications due to their lighter weight and ability to be molded into complex shapes.
One of the most important properties of engineering plastics is their chemical resistance. They have superior resistance to solvents and chemicals compared to traditional plastics such as PVC or polystyrene. This property makes them ideal for use in harsh chemical environments where other materials may fail or degrade quickly.
Another significant characteristic of engineering plastics is their dimensional stability. Unlike some traditional thermoplastics which tend to shrink or warp during processing, engineering plastics maintain their shape and size even after repeated exposure to high temperatures or stress. This property makes them suitable for use in precision components that require tight tolerances such as gears, bearings, and connectors.
Advantages & Disadvantages
Engineering plastics, also known as advanced or high-performance plastics, are a group of materials that exhibit superior mechanical and thermal properties compared to standard plastics. Their molecular structure is designed to offer excellent durability, strength, and resistance to extreme temperatures, chemicals, and UV radiation. Advantages of engineering plastics include their versatility in application, ability to replace metals in certain uses because of their high strength-to-weight ratio and ease of thermoforming.
On the other hand, one major disadvantage of engineering plastic is its cost. These materials can be more expensive than traditional plastic alternatives due to their complex manufacturing processes and higher quality standards. Additionally, some types of engineering plastics may have limited color options or poor aesthetics when compared with other materials like acrylics or polycarbonates.
Despite these drawbacks, the unique properties of engineering plastics make them ideal for a wide range of applications such as aerospace components, medical devices and automotive parts where durability under harsh conditions is essential.
Applications of Engineering Plastic
Engineering plastics are also known as advanced or high-performance plastics. They are a group of thermoplastics that possess superior mechanical and thermal properties compared to the standard plastics, such as polyethylene and polypropylene. These properties make engineering plastics ideal for use in a wide range of applications across various industries.
One application of engineering plastic is in the automotive industry. Here, they are used to replace metal parts due to their durability, heat resistance, and light weight. For example, polycarbonate is used for headlights and taillights due to its high impact resistance and transparency.
Another application is in the medical field where biocompatible engineering plastics like PEEK (polyether ether ketone) are used for surgical implants. This plastic has excellent strength, stiffness, and biostability making it ideal for implantation into the human body without causing any adverse reactions.
Overall, engineering plastic offers limitless possibilities when it comes to design flexibility thus making it an attractive choice for most manufacturers seeking high-performance materials that can withstand extreme conditions while delivering reliable performance over extended periods.
Other Names for Engineering Plastics
Engineering plastics are a type of plastic that has improved mechanical and thermal properties, making them suitable for use in various industrial applications. It is also known as performance or high-performance plastics. These materials are used to create products that require high levels of strength, durability, and resistance to temperature changes, chemicals, and other harsh environments.
Some common types of engineering plastics include acetal (POM), Nylon (PA), Polycarbonate (PC), Acrylonitrile butadiene styrene (ABS), Polyether Ether Ketone (PEEK), Polyphenylene oxide/polystyrene blend (PPO/PS) among others. Each of these materials has its unique set of properties that make them suitable for specific applications.
In conclusion, while engineering plastics may have different names depending on their specific properties or usage in industries; they all share the same trait – being strong and durable enough to withstand harsh environments making them ideal for industrial use.